The ‘Expert Q&A’ series highlights the experiences of practitioners and thought-leaders in the field of Emergency Management & Response.
Bryan Ayers is the Country Security Manager for GE-Alstom Power.
Omnilert: Tell us about Alstom Power.
Bryan Ayers: Alstom Power is a global company. We are based out of France. Our US operations involve a number of things- and I should say that we recently changed from Alstom to GE. A lot of Alstom was purchased by GE so some of the US operations are no longer part of our full menu of services. So for Alstom GE in the US we currently build large power plants. Everything from coal burning plants to hydro and steam turbine generators to all kinds of renewables including solar, wind, etc. We also have a grid component, which involves the distribution of the power that those facilities, we’ve constructed and operate, generate. We used to have a transport group, as well, that dealt mostly with rail, high-speed trains – that sort of thing – that stayed with Alstom. It was not part of the GE acquisition but in the past that transport group also used the services of Omnilert.
We have several thousand employees in the US and about 20+ facilities – from service centers to engineering and design facilities and production facilities. It’s a pretty large company.
Omnilert: Tell us a bit more about yourself- your background, current career initiatives, etc.?
BA: I am based in Windsor, Connecticut. I’ve been with the company since 1980, so 35 years. I began in the security department as a third shift Security Officer and eventually came up through the ranks of the security department and took on the role of Security Manager for a number of years for our facility in Windsor, Connecticut. At that time we were involved in the manufacturing of nuclear fuel and nuclear fuel rods at a very large campus with 23 buildings. Eventually I became the Emergency Services Coordinator, managing all emergency response and services for that large campus and then became the Country Security Manager in 2001 after the September 11th attacks. I was asked to helicopter up and look at all the facilities across the country to make sure we had consistent application of Alstom’s minimum security requirements and to make sure that our facilities were protected to the greatest extent in view of the September 11th attacks.
In 2003 I was given the responsibility to coordinate the Environment Health and Safety programs across the US to bring all of our facilities in line with a global environment health and safety initiative that Alstom had embarked on. So it was added to my responsibilities. In 2007 I also took on the responsibility of Ethics and Compliance Officer for the United States and handle all of our interactions with business advisers and consultants – anywhere that Alstom US businesses conducted business throughout the world.
I still do Country Security and I am still the EHS Coordinator. I did shed the US Compliance Officer role two years ago when we brought in a dedicated compliance officer. That is my journey.
Omnilert: How long have you been with the Alstom security team? Tell us about your team.
BA: 35 years total. In the US we have quite an extensive team that I deal with which is comprised of both Facility and Security Managers at different locations throughout the US. While I don’t oversee the specific programs at each facility, I provide general guidance on policy, minimum security requirements, and physical security at the sites.
I provide a lot of assistance with regard to our travel safety and security programs, specifically as it relates to employees traveling to sensitive places throughout the world. We do business pretty much anywhere including Afghanistan and Iraq, and other very difficult countries like Algeria and Egypt and other places throughout the world where there is a lot of security concerns. The most recent example would be the terrorist attacks in Paris. We had 22 US and Canadian employees in the country at the time, some who were in close proximity to the terrorist attacks. So after that occurred, I coordinated with our corporate security folks in Paris and with our travel coordinator to determine who was in the country, where they were, and reached out to them to get their status and offer assistance. We then provide reports to the country management team on the status of our folks.
.
Omnilert: What would you say was (or is) your biggest challenge and biggest success regarding security initiatives at Alstom?
BA: Biggest challenge was after September 11th. I always had to focus on the Windsor, Connecticut operations with some very minor involvement with the other Alstom US facilities at the time. So when September 11th occurred and I was asked to helicopter up and look at all of the facilities and bring everyone into some sort of consistent level of security, it was a pretty daunting task to reach out to all of the facilities and get a comfort level from the people I’d be working with- and getting them to comply with the minimum security requirements we had developed. But I am happy to say that as unfortunate as September 11th was, it actually allowed me to gain cooperation from folks who were obviously impacted, scared, and concerned with the security of their facilities. So tragic events typically cause people to look at what they’ve been doing and what they need to do going forward, and where you might have not had the cooperation on September 10th if I had embarked on that kind of role, September 11 really caused people to look for some assistance and cooperate much more than they would have. It was a significant challenge.
I would have to say my most significant success, in general, would be achieving the level of security that we now have across the country. Having the networks that we now have for ensuring that our employees are kept secure and that our safety programs are applied consistently. I am happy to report we have not had a fatality or serious injury in the US in a number of years and I think that has to do with the expertise we’ve developed within our EHS organization, the dedication of the folks on our team, the consistent application of the EHS programs and processes, and the oversight of those folks.
I think the testament to our success is we haven’t had fatalities or serious injuries. We get ahead of recalls and potential issues by looking at accidents in other places in the world and benefitting from a lessons learned kind of report and making sure we don’t have similar issues at our facilities in the US. I would say that is our greatest success – the achievement of a nation-wide level of security and safety.
It did take awhile to learn who all the players were and become familiar with the senior management and who their teams were locally. But again, because we had such a tragic event take place in the US I think people were far more willing to go ahead and participate in security surveys and then improvements- and that’s not to say there wasn’t resistance. In fact, a couple of facilities really felt they were secure enough, didn’t need anything, and didn’t want new security. But it’s funny because some of those facilities were the most difficult to convince, and now those that resisted actually ended up being some of our greatest ambassadors going forward.
Once they saw the level of security they now enjoyed, and the tools that were now at their disposal and embraced them, they became really good spokespersons for us as we moved to other facilities. Now we have a great network – they don’t hesitate to reach out when they have an issue or threat of violence at a facility. They know what my group is capable of doing in very short order and that things will be handled in confidence and that we do get results. It took some time but now I’m happy to say we have a pretty well rounded organization and I think we’ve demonstrated through our success that working with us is very worthwhile.
Omnilert: How long has Alstom utilized Omnilert?
BA: We have been involved with Omnilert for at least 10 years through me, but I know in the past there were individual facilities that participated in utilizing the services. In fact, the way I became aware of Omnilert was through a couple of facilities who were already engaged within the company. We were looking for some sort of emergency mass communications product and when I reached out to facilities they indicated they already had a relationship with Omnilert.
We looked at other providers and just didn’t find anyone that had the menu of services and the reliability of equipment and service that Omnilert did. We decided the system seemed to operate so well that we wanted to offer it to all facilities across the US so I entered into a national agreement with Omnilert for a very reasonable price that allowed us to deploy the Omnilert tool to facilities throughout the US.
Omnilert set up individual accounts for each facility and I then set up administrators and training, etc. I think the employees and folks at facilities that manage the Omnilert system are very appreciative that we do this on a central level. It doesn’t cost them anything – I pay for it out of our country security budget. We’ve established a lot of templates for signup sheets and communication to employees when we deploy the tool so we made it easy for them to apply it at their facilities.
So it’s been about ten years since I’ve been involved on a country level and that’s how it evolved to the individual facilities to a more national agreement. I established it with my budget and then deployed it individually through the US facilities.
Omnilert: You’ve already started to touch on this – Could you talk a bit more about how Omnilert is implemented at Alstom?
BA: We introduced the tool to facilities and let them know what the different methods of subscribing employees to the system are, and then we had a discussion with the facility on their preference based on how they should best proceed. I can’t say there is one way that is used at every facility – some of the facilities have chosen to do a mass upload and populate their own spreadsheets and work with Omnilert to subscribe everyone; other facilities have chosen to allow their personnel to subscribe on their own and have given them the link and instructional PowerPoint presentation we put together. Others use a very simple paper sign up process because they may have a different type of workforce.
They may not have a bunch of engineers working in offices that are skilled to go on an online database and sign themselves up. Some of these folks are machinists, maybe field service technicians that work out of their home and travel to sites for commissioning. There may be construction personnel who don’t have access to computers. We don’t prescribe to them how to sign up their folks. We give them the different menus of methods for getting folks involved, let them choose, and then assist them to insure they’ve captured the number of folks they intended.
Omnilert: Can you share a time Alstom has had to utilize the Omnilert system? What happened?
BA: I am aware of what happens at facilities across the US. One of the requirements that I do mandate is that I am included as a subscriber on any system that is deployed. So if there is a situation in Jupiter, Florida or Richmond, Virginia or anywhere, I will get a notification exactly the same as any of the residents of that facility. That helps me insure that I am aware of anything that’s going on at these facilities where they may not be thinking to notify me right off the bat, which is appropriate in an emergency situation. I want them to take care of their folks locally and implement their emergency response plan, so Omnilert really helps me to keep on top of what’s going on in facilities very quickly without having to wait on a phone call. I sleep well at night knowing I’m going to hear anything that goes on at any of our facilities and I like knowing that I have this tool available to properly communicate with our country management and our crisis management team. We even use it for our small groups at our Windsor campus for buildings spread out over Windsor and Bloomfield. It’s a great tool.
A good example, and the most recent example, of when Alstom had to utilize the Omnilert system would be the Paris terrorist attacks. I spent a lot of time reaching out to folks and communicating with people to make sure they were safe and didn’t require assistance or movement out of the area they were currently accommodated in. It happened over a weekend so it would’ve been quite a challenge to have to then reach out to our US country crisis response team and keep them all informed. Many of them may not be looking at email periodically on the weekend. Within the Omnilert system we set up a group called “US Crisis Response Team” and as the situation was unfolding we were reaching out to folks and achieving results. I would periodically send a message out to that entire team, comprised of about 35 people, to notify them of progress or issues we were experiencing. It gave me a high level of confidence that these folks were staying informed and I’m not having to rely on simply sending them an email on the Alstom network. I know they are getting it via text message on their phone and through whatever means they have subscribed to. Typically, those folks subscribe to every method we have available, so maybe a voice message to their home phone and cell phone, a text message, an email, etc. It made my job a lot easier while I’m reaching out to 20+ people at various locations throughout Paris. It was very easy to send a single message out and have a high level of confidence that I was reaching out and communicating with the entire crisis response team.
Omnilert: What advice would you give similar structured organizations in regards to emergency response plans and coordination?
BA: First off, you absolutely have to have a plan for dealing with an emergency or crisis. If you wait for the crisis or emergency to occur it’s too late and the only thing you will achieve is chaos. You need to ensure you have plans in place for the protection of your employees first and foremost, and then also for the protection of your facilities and assets. Without employees we don’t do business, but also without the tools and facilities for those employees to do their work we are even further from doing business. So you absolutely must have emergency plans, crisis response plans, and some sort of organization that responds when there is an emergency. That organization must be properly trained to deal with the types of incidents and emergencies that you may experience.
In my eyes, it’s very, very cheap insurance to deploy card access systems, alarm systems, and surveillance camera systems. Make them prominent. Don’t hide the fact that you have that security because those deterrents are some of the most effective means of preventing a crime at your facilities.
As part of your emergency plan and response plan, you need to have a way to communicate with employees to let them know what’s going on. Your employees have the right to know quickly and have an understanding of exactly what the situation is as it’s occurring. There’s nothing worse than having employees wandering around during an emergency, hearing things and seeing things they don’t understand, and not receiving some sort of communication about exactly what is occurring and what direction you want to provide to them. You need to have that kind of communication available – and that’s one of the more valuable tools of our emergency plan: the Omnilert system. Active shooter situation – you need a very effective and quick way to get the information out.
Once you have the communications system in place, don’t reserve it just for emergencies. Don’t overuse it so people start to ignore it and become complacent, but use it periodically as a test so that employees are able to determine all of their communication methods selected as part of their subscription are working. Maybe they’ve changed cell phones or cell phone providers and forgot to update us. A test triggers a thought in their mind to go back and change it. Any time we do a test we always get communication from employees asking for additional methods, or changes.
Lastly, similar to the communication system, exercise your plan from time to time. If you don’t have emergencies you need to sit down and do tabletop exercises or you need to exercise the plan to be sure the responders and everyone involved is fully aware of what their responsibilities are and have opportunity to act it out and practice. You can’t formulate a plan and then not have an emergency for two years or three years and then expect everyone to perform appropriately if you haven’t done periodic exercises and training.
All of that together lends itself to a corporation being able to properly respond to an emergency. I think companies have a responsibility to do that and ensure the safety and security of their employees. That would be my advice.
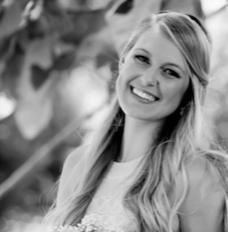